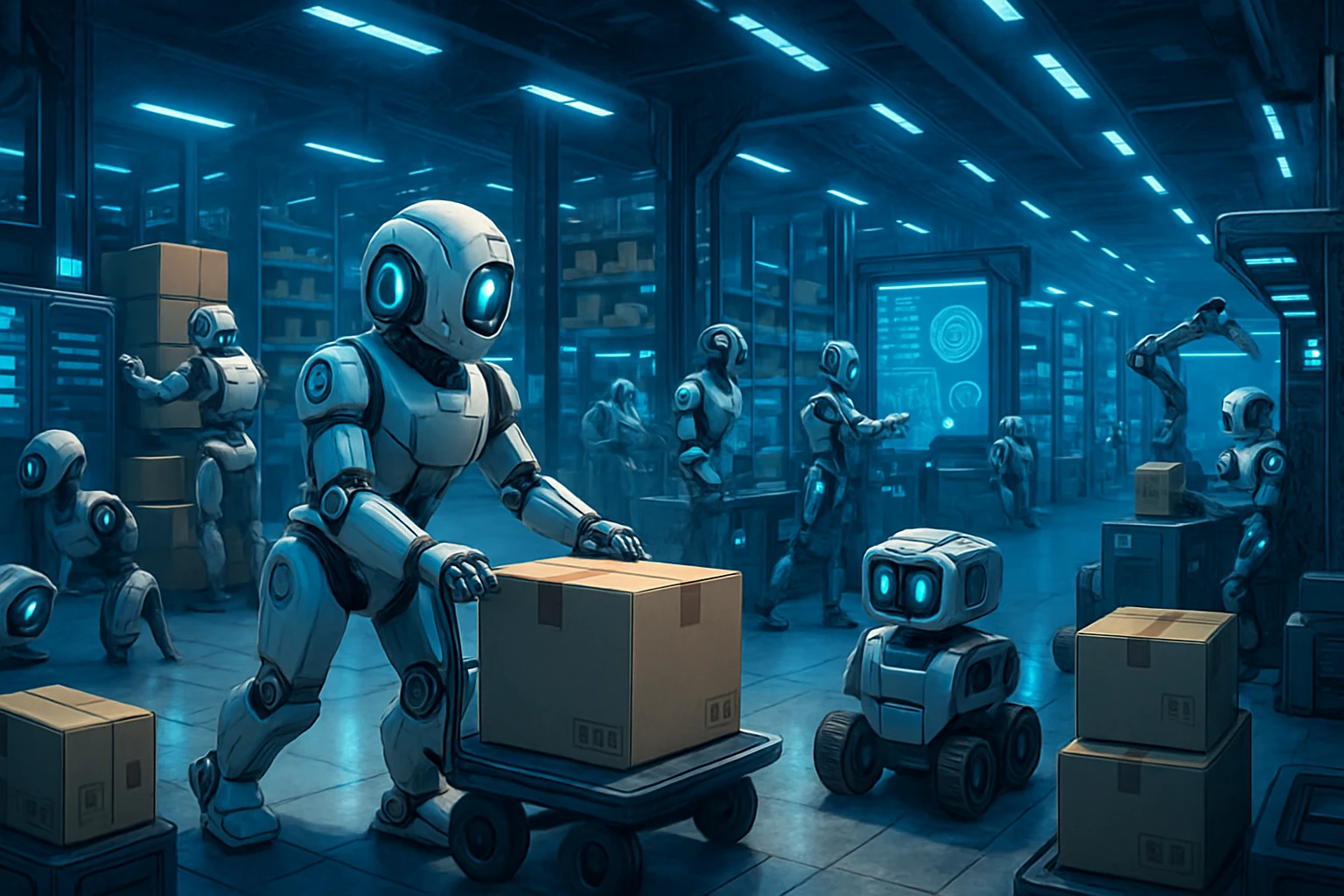
How Automation Is Disrupting Warehousing
Did you know that by the time you’ve finished reading this paragraph, an automated warehouse system somewhere has already picked, packed, and prepped an order for delivery? Yep, that’s how fast and efficient things have gotten. Welcome to the future of logistics—where machines don’t just help out, they hustle.
If you work in logistics, or you’re just geeking out over what tech is doing to our physical world (hi, fellow nerd 🙋), you’ve probably felt the shift. Warehousing isn’t what it used to be. Goodbye rows of clipboards and forklift traffic jams; hello intelligent bots, AI-powered route planning, and predictive inventory systems that somehow always know what’s about to run out before you do.
So, what’s the big deal? Well, traditional warehousing is kind of like trying to keep a hundred plates spinning at once. Labor shortages, human error, rising delivery expectations (thanks, next-day shipping), not to mention the constant pressure to drive down costs. It’s a lot. And that’s where automation in logistics swoops in like a superhero with a barcode scanner.
The Game-Changers in Warehouse Automation
I’ve seen first-hand how intimidating—and thrilling—this automation wave can be. A client I worked with recently implemented autonomous mobile robots (AMRs) to handle internal transport. Within weeks, they slashed their walking time by over 50%. People were less tired, picking was faster, and accuracy? Chef’s kiss. It was one of those “why didn’t we do this sooner?” moments.
If you’re wondering where to start, here are three solid, real-world ways automation is making warehouses smarter (and less chaotic):
- AI in warehouses: Modern AI isn’t just about number-crunching—it’s predicting demand, optimizing stock levels, and even detecting issues before they become problems. It’s like having a really smart co-manager who doesn’t sleep.
- Robotics for repetitive tasks: Think picking and packing bots, conveyor systems that smartly reroute items, or robotic arms lifting heavy stock. They’re faster, don’t get distracted, and never call in sick.
- Warehouse Management Systems (WMS) integration: Sync your software with your physical workflow. A good WMS connected to automation tools can reduce stock-outs, cut costs, and keep your team focused on less soul-crushing work.
Where We’re Headed
I get it—automation can sound like sci-fi meets corporate buzzword soup. But it’s real, it’s happening now, and it’s not just about the tech. It’s about freeing up time, reducing errors, and letting humans do what they’re best at—thinking big and solving problems.
The truth? Warehousing is entering its golden age. And whether you’re knee-deep in pallet racking or managing logistics from a cushy office chair, automation is your not-so-secret weapon for staying ahead in an increasingly competitive game.
So let’s dive deeper into this wild, wonderful world of warehouse automation—because waiting it out isn’t an option, but jumping in? That could change everything.
The Challenge: From Chaos to Order
Did you know the average warehouse worker spends nearly 7 weeks a year just walking around? That’s not 7 weeks of dancing or hiking—just moving back and forth trying to locate stuff.
Yep, welcome to the all-too-familiar world of warehouse chaos. If you’ve ever worked in logistics or managed inventory, chances are you’ve had one of those “Where on earth is that pallet of widgets?!” moments. I’ve personally seen seasoned pros dig through shelves, paperwork, and row after row of identical-looking boxes like they’re hunting buried treasure. Not exactly the most efficient use of time (or patience).
The Not-So-Fun Reality
Manual warehouse operations often feel like a game of constant catch-up. Whether it’s misplaced inventory, human error in tracking, or just trying to keep up with demand during a busy season, the old-school systems just can’t keep pace. And when the pressure’s on—say during peak shipping times—it turns into organized chaos at best, total meltdown at worst.
I once helped a client during Black Friday season. Their team of 15 was drowning in pick tickets, frantically yelling across aisles, and literally sprinting to find orders. They had the stock. Just not the system to make sense of it. Sound familiar?
Here’s Where Automation Steps In
Fortunately, there’s a better way—and it’s not science fiction. Warehouse automation is turning that chaos into calm, and here’s how:
- Smart Sorting Systems: Automated conveyor belts and sorting tech don’t just move items; they make sure each item goes exactly where it needs to go, fast. Think of it like a traffic controller that never sleeps and doesn’t make mistakes.
- Real-Time Inventory Tracking: With RFID tags and smart sensors, you always know what you have and where it is. No more guessing or double-counting. It’s like having a digital twin of your warehouse in your pocket.
- Automated Picking Solutions: Robots and pick-to-light systems help workers grab the right items with fewer steps and zero confusion. One company I consulted with cut their picking time by nearly 40% after installing a simple light-directed system.
Take Action
- Audit your current workflow—Where are delays or errors happening most?
- Start small: Implement one automation (like barcode scanning or pallet tracking) and test results.
- Train your team: Automation supports people—it doesn’t replace them. Empower them to use the tools.
From Stress to Strategy
Look, transforming your warehouse doesn’t mean flipping a switch overnight. But small, strategic steps toward automation can create big wins over time. Imagine walking into your facility and knowing things are running smoothly—even during your busiest season.
It’s not just about cutting costs or saving time (though hey, those are pretty great, too). It’s about working smarter, cutting the chaos, and building a warehouse operation that actually works for you. We’re not talking about the future—it’s already happening. And you’ve got a front-row seat.
Let’s leave the chaos behind—order is just a few smart moves away.
Unleashing AI: The Brain Behind the Brawn
Did you know that AI can predict inventory demand with up to 95% accuracy? Yep. It’s not some pie-in-the-sky futuristic thing—it’s happening right now in warehouses just like yours. Honestly, if AI were a person, it’d be the employee who shows up early, never complains, and can somehow read your mind. Dream hire, right?
Let’s be real for a sec. Warehouse operations can feel like organized chaos. Between tracking fluctuating inventory, dealing with unexpected delays, and praying that no one misplaces a high-value item, sometimes it’s pure controlled panic. I’ve talked to managers who carry actual stress balls in their pockets—I mean, I get it.
That’s where AI becomes the power behind the scenes—the wizard pulling the levers of smarter, faster, and more accurate operations. And it doesn’t just help, it transforms how warehouses function from the ground up.
So, how exactly is AI flexing its brainpower in real-life warehouses?
- Predictive Analytics = Fewer Surprises
AI dives into your historical data and seasonality trends to forecast demand before orders even come in. Think of it like having a crystal ball—but without the weird incense. One of my clients cut their overstock by 30% in just two months by plugging AI into their inventory system. Less waste, happy finance team! - Smart Sorting & Routing = Lightning Speed
Machine learning algorithms are out here playing traffic cop—optimizing pick routes for workers or bots so they’re not zigzagging across the warehouse like they’re in a game of human Frogger. The result? Faster picks and less fatigue. One facility shaved 20% off their average pick time just by letting AI do the route math. - Error Reduction = Sweet, Sweet Accuracy
From barcode scanning to visual recognition, AI helps double-check what’s being picked and packed. It’s like spellcheck, but for orders. Say goodbye to “oops, wrong item” returns. One major e-commerce brand saw 40% fewer packing errors after implementing an AI-based validation system. That’s no small win.
Here’s what you can do right now:
- Start small. You don’t need to overhaul your whole system overnight. Begin with predictive analytics—most WMS platforms now have some AI plug-ins or integrations.
- Map your current processes and see where AI fits naturally. Any repetitive, data-heavy task is prime AI territory. Picking sequences, stock level alerts, and even equipment maintenance ops are a good bet.
- Choose AI tools with solid track records. Don’t just jump on a fancy dashboard because it looks slick. Look for providers offering real warehousing use cases with proven ROI.
The beauty of AI? It doesn’t replace your team—it supercharges them. Frees up your people to focus on strategic work instead of chasing pallets and playing guessing games. You get fewer errors, faster operations, and better insights—without burnout.
If you’re still thinking AI is just a trendy buzzword, I’ve got news—it’s already behind the brawn, running the show. And the sooner you bring it into your warehouse world, the sooner you’ll wonder how you ever lived without it.
The future’s not just automated—it’s intelligent. Let’s make your warehouse part of that smarter tomorrow.
Robotics: More Than Just Fancy Gadgets
Did you know a single warehouse robot can process up to 300 orders per hour—while most human workers average around 60? Wild, right? We’re not talking about shiny, intimidating, sci-fi machines anymore. These are real, quiet, hardworking robots whirring alongside humans, lifting the weight (literally and figuratively) in warehouses around the globe.
I remember visiting a mid-sized distribution center not long ago. It wasn’t a huge Amazon facility with jaw-dropping tech everywhere. Just a regular warehouse. But what struck me was this little fleet of squat, Roomba-like robots zipping between shelves, pulling inventory, and dropping it off for packing—no moody sighs, no coffee breaks, just this laser-focused efficiency. It felt like watching a beehive where the bees have GPS.
So, why are robots such a big deal in warehousing now?
Let’s face it—warehouse work is tough. Repetitive movements, tight deadlines, shifting priorities. It’s physically exhausting and, let’s be honest, kinda dull sometimes. Plus, with supply chains needing to run like clockwork (especially after the last few years of chaos), performance has to be razor sharp.
Enter robotics. They’re not here to replace the entire workforce. At least, not yet. But they are making life a whole lot easier for the humans already there.
What can these bots actually *do*?
More than you’d think! Here’s how robots are quietly taking warehouses to the next level:
- Smart Sorting: Autonomous mobile robots (AMRs) now navigate the floor, identifying and picking items more accurately (and faster!) than humans. No more aisle wandering.
- Pack Like a Pro: Robotic arms with suction and gripper tech are packaging goods with fewer mistakes—and fewer broken mugs, trust me.
- Transport Mission: Go: Need to move inventory from dock to shelf? Let your robots do the heavy lifting without injuries or delays.
Pro tip: Start small. One growing trend is companies leasing robots as a service (RaaS—yep, it’s a thing). It’s like the Netflix of robotics. No upfront cost, easy scaling. Dip your toes in before doing a full tech overhaul.
And the ROI? Oh, it’s real. One case study I came across showed a mid-sized warehouse boosting throughput by 200% after deploying just 12 sorting robots. Plus, error rates dropped, and staff injuries went down too. People got to shift into less back-breaking roles. Win-win!
The Bottom Line: Robotics Are Your Warehouse’s New MVP
So yeah, what once seemed futuristic is now downright practical. Robotics in warehousing isn’t about showing off the latest toys—it’s about staying competitive, easing burnout, and making operations smoother than ever. Best of all? You don’t need to be a tech wizard to start.
Ready to bring some robotic reinforcements into your workflow? Take that first step. Your team—and your timeline—will thank you.
The Future: A Glimpse Into Next-Gen Warehousing
Did you know that by the time you finish this paragraph, over 500 new IoT devices will have connected to the internet? Wild, right? And yes—you guessed it—many of them are transforming warehouses as we speak.
If you’ve ever walked through a warehouse and thought, “There has to be a smarter way to do this,” you’re not alone. Trust me, I’ve been there, getting flashbacks of manually scanning pallets while hunting for that one elusive shipment. Traditional warehousing has long been a game of spreadsheets, forklifts, and guesswork. But that’s all changing. Fast.
We’re talking about a full-on glow-up for the warehousing industry—smarter, greener, and a whole lot cooler. Let’s take a peek at what’s shaking things up.
1. IoT Integration: From Guesswork to Precision
Imagine your warehouse talking to itself… in real time. That’s IoT (Internet of Things) in action. Sensors on shelves. Smart trackers monitoring humidity levels for sensitive goods. Pallets that report their own location. It’s not sci-fi—it’s already happening.
- Start small: Try integrating smart shelves or RFID tracking to reduce misplacements and shrinkage.
- Make it proactive: Use temperature and vibration sensors for perishable or fragile items to avoid costly surprises.
- Centralize data: Link your IoT network to a warehouse management system (WMS) with real-time dashboards.
My personal favorite use case? Smart forklifts that not only navigate busy warehouse floors but share data with the system to flag restocking needs before a human even notices. *Chef’s kiss*
2. Sustainability Solutions: Yes, Warehousing Can Be Green
Eco-friendly and logistics? Yep, it’s a thing now—and it’s becoming a competitive edge. Warehouses are huge energy consumers, but smart solutions are helping us turn that around.
- Go solar: Installing solar panels can offset energy use (and impress eco-conscious clients).
- LED and motion-sensor lighting: Seriously—why light up empty aisles 24/7?
- Cut packaging waste: Automated picking systems optimize packaging so you’re not shipping air (and paying for it).
I toured a warehouse recently where the whole facility ran on solar and had a zero-waste packing station. Not only was it cost-effective—they actually won a logistics innovation award for it. Win-win!
3. Advanced Logistics Tech: The Brain Behind the Operation
Imagine an AI system that predicts inventory needs, automates reordering, and even schedules your team based on demand peaks. AI and machine learning aren’t just buzzwords—they’re like having a logistics wizard in your server room.
- Use demand forecasting: Reduce overstock and out-of-stock by letting AI crunch the data.
- Add robotics: Autonomous mobile robots (AMRs) are streamlining picking processes and reducing injury risks.
- Test digital twins: Use simulations to design efficient layouts or test process changes before moving a single box.
Toss in blockchain-powered supply tracing and predictive maintenance for your machinery, and suddenly your warehouse has levels of insight that would’ve blown minds just a decade ago.
So… Is This “Next-Gen” Thing Really on the Way?
Absolutely—and it’s not some distant dream. These innovations are already being rolled out in forward-thinking warehouses. And as costs drop and tech becomes more accessible, this won’t be the exception. It’ll be the new standard.
So, if you’ve been wondering whether it’s worth keeping an eye on these trends, I say: don’t just keep an eye—get ready to sprint. Because the future of warehousing isn’t coming… it’s already knocking.
Action step: Start by picking one area—be it sustainability, tracking, or automation—to modernize. You don’t need to leap. Just take the first step. Your future warehouse (and your sanity) will thank you.
Embrace the Future: Transform Your Warehouse
Did you know that warehouses using automation tech see up to a 30% boost in productivity within the first year alone? That’s not just a little gain—that’s an operational glow-up!
I get it—when you’ve been running your warehouse a certain way for years, the thought of flipping the script with AI, robotics, and IoT gadgets can feel… well, like walking into a sci-fi movie. But here’s the thing: warehouse automation isn’t just for the Amazons or FedExes of the world anymore. It’s becoming accessible, even essential, for operations of *all* sizes.
Maybe you’ve felt the pain of late shipments because products were in the wrong bin, or watched your team hustle nonstop during peak season only to end up behind anyway. I’ve chatted with managers who spend hours buried in spreadsheets just trying to predict stock needs—and still miss the mark. Sound familiar? You’re not alone.
Let’s Break It Down: How to Start Automating (Without Losing Your Mind)
Automation doesn’t have to be all-or-nothing. You can start small and scale smart. Here’s what I recommend:
- Start with data. Take a good, hard look at your workflow. Where are the breakdowns? Is it inventory management, picking, or packing? Knowing the gaps helps you target automation where it matters most.
- Integrate smart sensors and IoT devices. These can track inventory levels in real time, alert your team to slowdowns, and even predict when equipment needs maintenance—before it breaks down. No more scrambling.
- Dip your toe into robotics. Autonomous mobile robots (AMRs) can help with repetitive tasks like transporting goods around the warehouse. They’re surprisingly cost-effective and easy to integrate.
One company I worked with introduced just six AMRs to assist their picking team. Within three months, picking speed increased by 40%, and error rates? Cut in half. It didn’t break their budget—and it sure didn’t break their backs.
The Future’s Here—Are You In?
Here’s what’s wild: we’re only scratching the surface. When AI, IoT, and robotics all work together, your warehouse doesn’t just get more efficient—it becomes *intelligent*. Think predictive restocking, optimized floor layouts based on real-time data, and fewer nasty surprises during peak season.
So if you’ve been wondering whether automation is worth the leap, let me tell you—this isn’t just about keeping up anymore. It’s about stepping up. You’re not replacing your team; you’re empowering them. You’re not losing control; you’re gaining more of it—with less stress in the process.
Start small. Think big. Embrace the future one upgrade at a time. Your warehouse—and your team—deserve it.